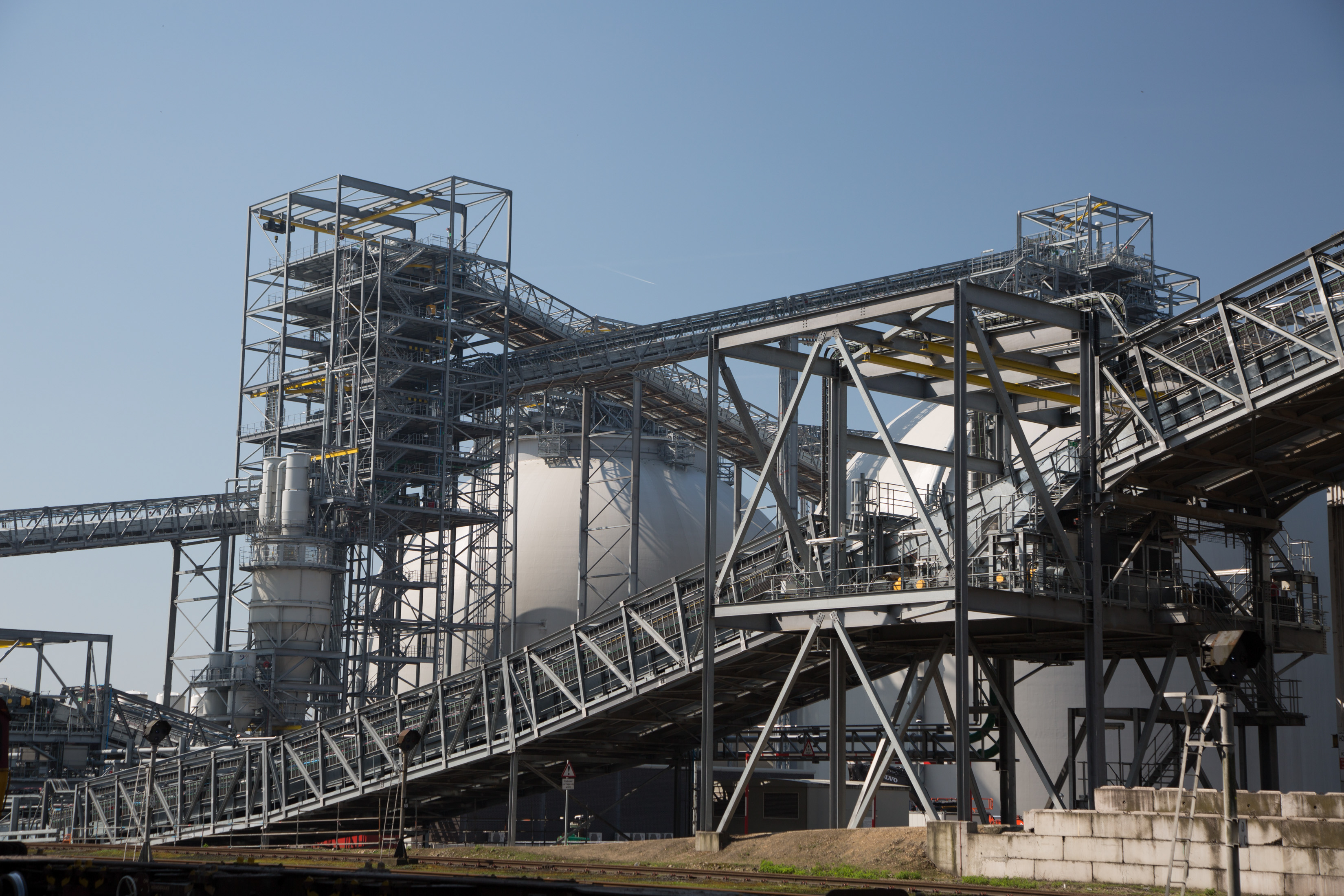
Humans have used wood as a source of fuel for over a million years. Modern biomass power, however, is a far cry from human’s early taming of fire and this is down to constant research and innovation. In fact, today it’s one of the most extensively researched areas in energy and environmental studies.
With biomass accounting for 64% of total renewable energy production in the EU in 2015, the development isn’t likely to stop. Ongoing advancements in the field are helping the technology become more sustainable and efficient in reducing emissions.
Here are seven of the projects, businesses, ideas and technologies pushing biomass further into the future:
Torrefaction – supercharging biomass pellets
When it comes to making biomass as efficient as possible it’s all down to each individual pellet. Improving what’s known as the ‘calorific value’ of each pellet increases the overall amount of energy released when they are used in a power station.
One emerging process aiming to improve this is torrefaction, which involves heating biomass to between 250 and 300 degrees Celsius in a low-oxygen environment. This drives out moisture and volatiles from woody feedstocks, straw and other biomass sources before it is turned into a black ‘biocoal’ pellet which has a very high calorific value.
This year, Estonian company Baltania is constructing the first industrial-scale torrefaction plant in the country with the target output of 160,000 tonnes of biocoal pellets per year. If it’s successful, power stations worldwide may be able to get more power from each little pellet.
bio-bean – powered by caffeine
Biofuels don’t just come from forest residues. Every day more than two billion cups of coffee are consumed globally as people get themselves caffeinated for the day ahead. In London alone, this need for daily stimulation results in more than 200,000 tonnes of coffee waste produced every year. More often than not this ends up in landfills.
bio-bean aims to change this by collecting used coffee grounds from cafes, offices and factories and recycling them into biofuels and biochemicals. The company now recycles as much as 50,000 tonnes of coffee grounds annually while one of its products, B20 biodiesel, has been used to power London buses. bio-bean also produces briquettes and pellets, which, like woody biomass, can serve as an alternative to coal.
Biomass gasification – increasing the value of biomass waste
Biogas is often seen as a promising biofuel with fewer emissions than burning fossil fuels or biomass pellets. It’s an area undergoing significant research as it points to another means of creating higher-value products from biomass matter.
The Finnish town of Vaasa is home to the world’s largest gasification plant. The facility is part of a coal plant where co-firing biogas with coal has allowed it to reduce carbon dioxide (CO2) emissions by as much as 230,000 tonnes per year.
As well as reducing emissions, co-firing allows the power plant to use 25% to 40% less coal and when demand is low in the autumn and spring months, the plant runs entirely on biogas. More than that, the forestry residues which are used to produce the biogas are sourced locally from within 100 km of site.
(As part of our transition away from coal, co-firing biomass with that fossil fuel took place at Drax Power Station from 2003 until full unit conversions became a reality in 2013.)
Lynemouth Power Station – powering the move away from coal
After 44-years, the coal-fired Lynemouth Power Station in Northumberland is the latest UK power producer converting to biomass-fuel. Set for completion this year, the plant will supply 390 MW of low-carbon electricity to the National Grid, enough to power 700,000 homes.
Every new power station conversion poses different challenges as well as the opportunity to develop new solutions, but none are as crucial as the conversion of the materials handling equipment from coal to biomass pellets. While coal can sit in the rain for long periods of time and still be used, biomass must be kept dry with storage conditions constantly monitored and adjusted to prevent sudden combustion.
At Lynemouth the handling of 1.4 million tonnes of biomass annually has required the construction of three, 40-metre high concrete storage silos, as well as extensive conveyor systems to unload and transport biomass around the plant.
BioTrans – two birds with one stone
Energy and food are both undergoing serious changes to make them more sustainable. Danish startup BioTrans is tackling both challenges by using one of the food industry’s key pain points – wastage – to create energy with its biogas systems.
The company installs systems that collect leftover food from restaurants and canteens and stores it in odour-proof tanks before collecting and turning it into biogas for heating and electricity production. More than just utilising this waste stream, the by-product of the gasification process can also be sold as a fertiliser.
Drax and C-Capture – cutting emissions from the source
Carbon capture, usage and storage (CCUS) is one of the most important fields in the energy sector today. The technology’s ability to capture CO2 from the electricity generation process and turn it into a revenue source before it can enter the atmosphere means it’s attracting significant investment and research.
Drax is partnering with C-Capture, a company spun out of the University of Leeds’ chemistry department, to trial a new form of CCUS. The pilot scheme will launch in November and aims to capture a tonne of CO2 per day from one of Drax’s biomass units.
C-Capture’s technology could make the process of capturing and storing CO2 less costly and energy intensive. It does this using a specially developed solvent capable of isolating CO2 before being recycled through the system and capturing more.
If the pilot proves successful, the technology could be implemented at an industrial scale, seeing up to 40% of the CO2 in the flue gases from Drax’s biomass units captured and stored. If the technology tested at Drax leads to the construction of a purpose-built carbon capture unit elsewhere, scientists and engineers at C-Capture believe the CO2 captured could exceed 90%.
Back in North Yorkshire, the eventual goal is negative carbon emissions from Drax Power Station – its biomass units already deliver carbon savings of more than 80% compared to when they used coal. And if a new revenue stream can be developed from the sale of the carbon captured then the power produced from biomass at the power station could become even more cost effective.
With thanks to Biomass UK and The European Biomass Association (AEBIOM).