Sourcing sustainable biomass
Our climate positive, nature positive, and people positive sustainability outcomes will only be delivered by sourcing, producing and using the right biomass.
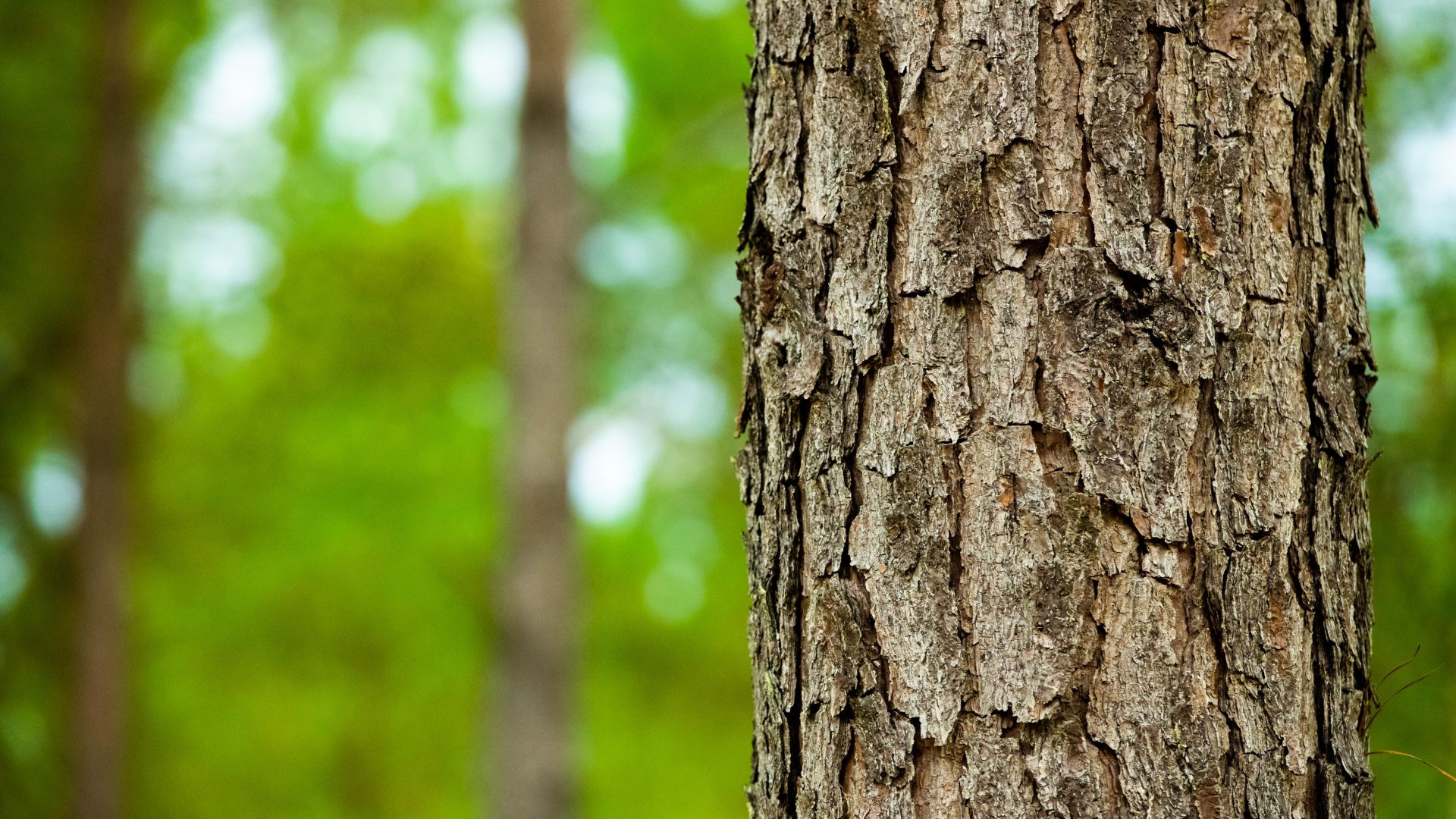
Biomass sourcing
Drax has been working with biomass for over 20 years. We began co-firing biomass with coal in 2002 and completed our first full conversion of a coal unit to biomass in 2013.
Our sustainability due diligence process is designed to ensure the biomass we use for generation at Drax Power Station is sustainable and compliant with relevant legislation. Woody biomass supplier compliance is evidenced by external certification schemes, alongside our internal assurance system and third-party audits commissioned by Drax.
Our Group Sustainability Policy and Supplier Code of Conduct outline our requirements and are evidenced and included in biomass supplier contracts.
Our Biomass Sustainability Requirements
We adhere to the UK Government criteria for sustainable biomass, the Forest Europe Sustainable Forest Management criteria and we comply with the UK Timber Regulation (UKTR).
- Group sustainability policy – in place since 2008, our policy covers our core sustainability values on protecting biodiversity, reduction of greenhouse gas emissions and contribution to social values.
- UK Government criteria for sustainable biomass – we report monthly on compliance with the UK sustainability criteria, including life cycle emissions limits and the land criteria. This covers the requirements of the Forest Europe Sustainable Forest Management criteria, including: maintaining forest area and carbon stocks; encouraging the production of forest products; maintaining the health and vitality of the forest ecosystem; conserving and enhancing biological diversity; contributing socio-economic benefits; and ensuring that soil and water protection is maintained.
- UK Timber Regulation – The UKTR applies from 01 January 2021 and the requirements remain the same as under the European Union Timber Regulation (EUTR).
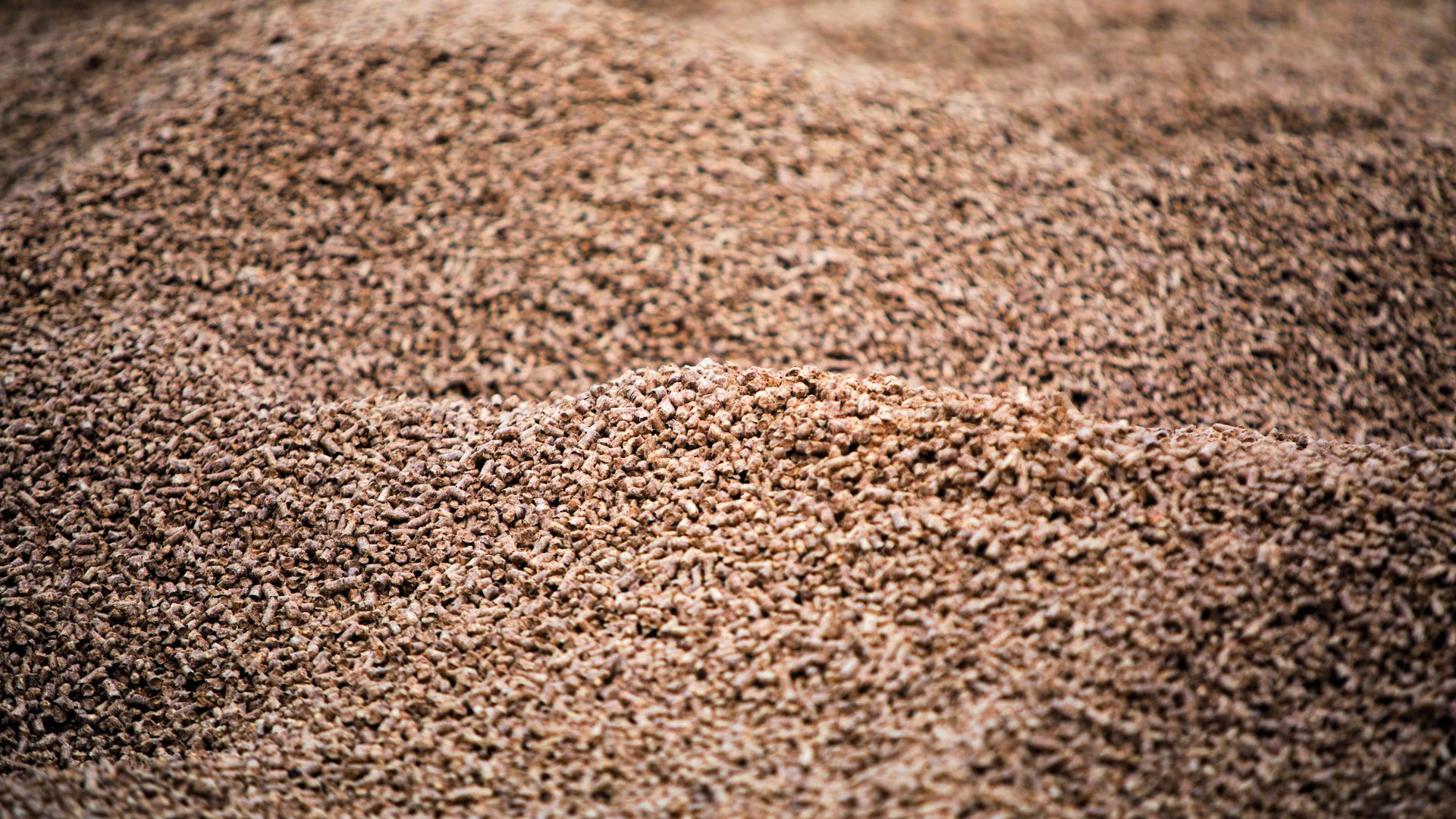
Responsible Sourcing Policy for Biomass
Further to our Group Sustainability Policy, our Responsible Sourcing Policy for Biomass outlines our forest biomass sustainability commitments. The policy strengthens our approach in line with recommendations made by a report commissioned by the European Climate Foundation. This is to provide further assurance that the sustainable biomass we source makes a net positive contribution to climate change, protects and enhances biodiversity and has a positive social impact on local communities.
Our forest biomass sustainability commitments:
- We will reduce carbon dioxide emissions
We are committed to ensuring our use of biomass makes a positive contribution to tackling climate change and fulfilling the UK’s net zero by 2050 target.
- We will protect the natural environment
We recognise our duty to keep forests thriving and to respect the many benefits they bring, including carbon storage, protection of soil and water quality, supporting biodiversity and provision of habitat.
- We will support people and communities
From state-owned forests to smallholdings, and from the US southeast to the Baltic states, forest owners, forest workers and communities in our sourcing areas are bound by their common reliance on forests for employment, wellbeing and quality of life.
- We will invest in research, outreach and intervention
The strength of our collaboration with others will improve the sourcing choices we make. We are committed to working with governments, non-governmental organisations, academia and other stakeholders to continually improve biomass sourcing and develop best practice.
Due Diligence
Our sustainability due diligence process is designed to ensure the biomass we use for generation at Drax Power Station is sustainable and compliant with relevant legislation. Woody biomass supplier compliance is evidenced by external certification schemes, alongside our internal assurance system and third-party audits commissioned by Drax.
Governance
The Group Director of Corporate Affairs has overall responsibility for delivering Drax Group’s sustainability performance and ensuring biomass meets the Government’s sustainability criteria. Cases requiring special attention are escalated to the Group Ethics and Business Conduct Committee (EBCC) or the Executive Committee. The Independent Advisory Board on Sustainable Biomass [link https://www.drax.com/sustainability/independent-advisory-board-on-sustainable-biomass/] established in 2019 provides advice on sustainable biomass and its role in Drax’s transition to net zero emissions.
As part of our sustainability due diligence process, raising concerns to our committees is one method we use to mitigate risk. This is dependent on the level of risk within the supply chain and geography, and outcomes from independent commodity and country risk assessment reports. In 2021, two matters regarding prospective alternative fuel supply country-level risks were escalated to the Group EBCC or the Executive Committee. This process ensures potential risks are appropriately scrutinised and that additional measures and requirements are implemented, as appropriate.
Due Diligence Process
Drax has developed a rigorous process to ensure that new and existing biomass suppliers demonstrate that all necessary sustainability and legal requirements are met. Our key stages for ensuring compliance include: chain of custody; supplier audits; the UKTR legality assessment; GHG life cycle assessment and monitoring; the sustainability data return (SDR) captured in the contract; the SDR and annual declaration; regional and country risk assessments; and supplier relationship management and monitoring. These stages are implemented in an ongoing cycle to provide robust evidence across each element.
Our due diligence process always begins with a regional risk assessment, which identifies high-level risks such as deforestation or illegal logging, corruption and issues with workers’ rights. This ensures that we focus on these high risks and how they are being mitigated. These reports are renewed every three years, or more frequently if there are causes for concern, to ensure that we always stay on top of developing issues.
This is followed by the SDR, where we ask the supplier 43 detailed questions about all aspects of their supply chain and to provide documentary evidence to support their answers. This sustainability declaration subsequently forms part of the contract between Drax and the supplier.
Third-Party Audits
Each new supplier is subject to an independent audit commissioned by Drax before pellets can be delivered. Existing suppliers are audited at least once every three to four years. The audit requires the supplier to pass a series of detailed environmental and social checks along the whole length of their supply chain and pellet manufacturing process. Findings are categorised as high, medium or low priority.
High-priority findings can result in termination of a supplier agreement. Medium-priority findings result in the supplier being given a deadline for rectifying them. Low-priority issues highlight areas where our independent auditors believe there is scope for the supplier to improve their practices. Drax engages with our suppliers to share best practice and support and encourage improvements to procedures.
The Sustainable Biomass Program
Suppliers can evidence the necessary sustainability requirements through Sustainable Biomass Program (SBP) certification, a certification system for woody biomass.
SBP-certified material has been benchmarked by Ofgem to fully meet the UK sustainability requirements. We encourage our suppliers to progress from our own checks and third-party audits commissioned by Drax towards SBP certification. In 2021, 98% of the woody biomass we sourced for use at Drax Power Station was SBP compliant.
The Sustainable Biomass Program
Forest Management Certification
In addition to our own checks, third-party audits commissioned by Drax and SBP certification, sustainability can also be demonstrated through the Forest Stewardship Council® (FSC®) – Drax FSC License Code: FSC-C119787 – and PEFC’s Forest Management (FM) certification. These schemes are global not-for-profit organisations dedicated to the promotion of responsible forest management worldwide. FM certification process confirms that the forest is being managed in a way that preserves the natural ecosystem and benefits the lives of local people and workers, while ensuring that it sustains economic viability.
FM certification may be difficult to achieve for some types of forest owners and, for this reason, a secondary level of FSC certification called Controlled Wood is available. This ensures that wood fibre is not: illegally harvested; harvested in violation of traditional and human rights; harvested in forests in which high conservation values are threatened by management activities; harvested in forests being converted to plantations or non-forest use; or from forests in which genetically modified trees are planted.
Chain of Custody
Once certified, Chain of Custody can be used as a mechanism for tracking wood fibre from the forest to the final product and destination. Each supplier in the chain must have a documented system that enables the supplier to demonstrate that the wood fibre has been identified and separated from non-certified and non-controlled wood at each stage in the supply chain. Drax requires that all of its suppliers achieve Chain of Custody certification before contracts are signed and pellets can be delivered.
At Drax, our key biomass buyers, logistics, legal and communications colleagues are required to complete Chain of Custody training with the sustainability team.
Supplier Engagement
Drax operates a proactive supplier engagement programme to develop closer relationships with all biomass suppliers on sustainability issues. Our approach includes regular site visits to improve overall performance by identifying any potential risks, understanding constraints and capacity, monitoring audit findings and corrective actions, carrying out training and providing resources as required.
Biomass Sources in 2022
Biomass supply chain transparency is a key element of our approach and we provide additional supply chain information at Drax ForestScope www.forestscope.info.
We respond annually to the CDP Forests questionnaire and achieved a rating of B in 2022.
In 2022 our biomass was sourced from established, responsibly managed working forests in the US South, Canada, Europe, Brazil and Russia. Drax Group, Pellet Production, and Drax Power Station sources of fibre are disclosed in our ESG Performance Report.