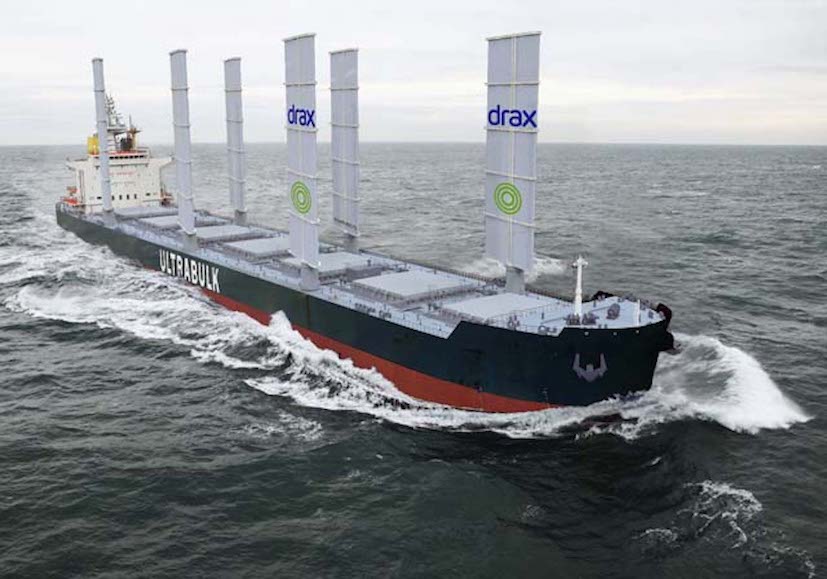
Key takeaways:
- Drax’s ambition of becoming a carbon negative company by 2030 means we’re always working to reduce our supply chain emissions further.
- We’re partnering with different organisations to explore innovative solutions to lowering shipping emissions.
- Through our experience of carbon capture and storage, we can deploy the technology to decarbonise operations at our pellet mills.
- Using rail wagons specifically designed to transport biomass wood pellets helps us reduce transport on land emissions.
- By developing a new BECCS power station in the U.S., we can help decarbonise electricity systems while removing emissions from the atmosphere and tackling climate change.
At Drax, we have ambitious plans to not only help countries around the world replace fossil fuels with renewable biomass, but to become a carbon negative company by 2030.
For the world to achieve its net zero targets and meet the Paris Agreement goals of keeping global temperature rises below 1.5°C, it’s essential to remove more carbon from the atmosphere than is produced.
Drax is leading in this effort through pioneering bioenergy with carbon capture and storage (BECCS) technology. BECCS is the process of generating renewable power using sustainably sourced biomass while capturing and permanently storing CO2.
Developing BECCS at scale and achieving our own carbon negative objective means working to decarbonise the technology’s entire supply chain. It’s a responsibility we’ve been committed to for decades, even before the Drax Power Station was converted to run on sustainable biomass, and we continue to look for new innovations.
Here are three of the ways we’re working to optimise our supply chains to make them as energy efficient and low-carbon as possible:
1. Shipping emissions: Harnessing the wind
Around 90% of the world’s goods are transported by sea, including the wood pellets produced at our pellet mills and used to generate renewable power at Drax Power Station in the U.K. And while shipping has a lower carbon footprint than road or air transport, the sector still accounts for around 3%, or 1 billion tonnes of global greenhouse gas (GHG) emissions. Initiatives to reduce the emissions associated with shipping are an important part of our efforts to decarbonise our supply chain and become carbon negative.
In 2022, we signed a memorandum of understanding with Japanese shipping company MOL Drybulk. Together, we’re exploring installing MOL’s proven Wind Challenger hard sail technology on vessels transporting wood pellets on routes such as British Columbia to biomass customers in Japan. Wind Challenger, which reduces fuel consumption and emissions by harnessing wind power through modern sails, could be ready to be fitted onto newly built vessels for Drax from 2025.
The Environmentally Friendly Bulk Carrier “EFBC” project’s use of new and more efficient wind-power could contribute to reducing emissions associated with shipping biomass by around 20%. At a later stage, the project could also incorporate the use of other low-carbon technologies, as well as lower-emission fuels such as liquefied natural gas, ammonia, and synthetic fuels.
We previously partnered with the Smart Green Shipping Alliance, dry bulk cargo transporter Ultrabulk, and Humphreys Yacht Design for a feasibility study that looked at reducing shipping emissions. The study examined the potential to retrofit an innovative sail solution known as FastRig onto Ultrabulk ships importing biomass into the UK. FastRigs, made from 100% recycled and recyclable material, are designed to considerably reduce GHG emissions and the use of fuel. The feasibility study found that the FastRig solution could help lower fuel use and GHG emissions on one of our export routes – from Baton Rouge, Louisiana, to Liverpool in the UK – by at least 20%.
2. Reducing emissions through carbon capture and storage
Biomass pellet plants are a key part of Drax’s supply chain. By producing renewable, sustainable biomass feedstock we can help countries around the world to replace fossil fuels.
Our pellet mills in Canada and the U.S. South use a mix of fibre sources – all of which are unsuitable for lumber or other solid wood products. Globally, in the first half of 2022, almost 70% of the fibre for our biomass came from sawmill residues, like sawdust and wood chips.
Fibre for biomass also comes from low-grade wood that’s rejected by the lumber industry, slash left over from lumber industry harvests, and trees removed in forest management processes, like thinning and wildfire mitigation.
The pelletisation process uses power from local grids – wedding us to regional power sources. In areas like the U.S. where 61% of electricity is still generated from fossil fuels, this adds to our Scope 2 emissions.
However, our pioneering development of carbon capture technology offers the potential to decarbonise emissions connected to pelletisation. It’s one of the ways that the experience and technology we put into action at a new U.S. BECCS plant can decarbonise other facilities, whole industrial clusters, and our own supply chains.
3. Rail: The low-carbon road option
For in-country transportation, Drax utilises rail freight as much as possible, as rail offers the capacity we need as well as having a lower carbon footprint than road transport. In the UK, we own 225 rail wagons, specifically designed to transport biomass wood pellets and will be taking delivery of 30 more in 2023. The bespoke wagons carry a greater volume of compressed wood pellets than traditional wagons are capable of, delivering around 20,000 tonnes of renewable biomass to Drax Power Station every day.
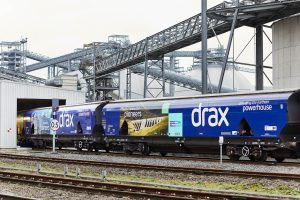
Train carrying sustainably sourced compressed wood pellets arriving at Drax Power Station in North Yorkshire [click to view/download]
In 2020 a new rail link was opened to connect our LaSalle BioEnergy biomass pellet plant in Louisiana to the regional rail network, enabling the delivery of around 7,000 tonnes of biomass per week to the Port of Greater Baton Rouge. The rail link replaced the 27 tonnes that was previously transported by each individual truck.
Helping countries around the world achieve net zero and working towards becoming a carbon negative company is only possible if we continue our practice of examining our supply chain and developing new innovative ways to reduce emissions even further.