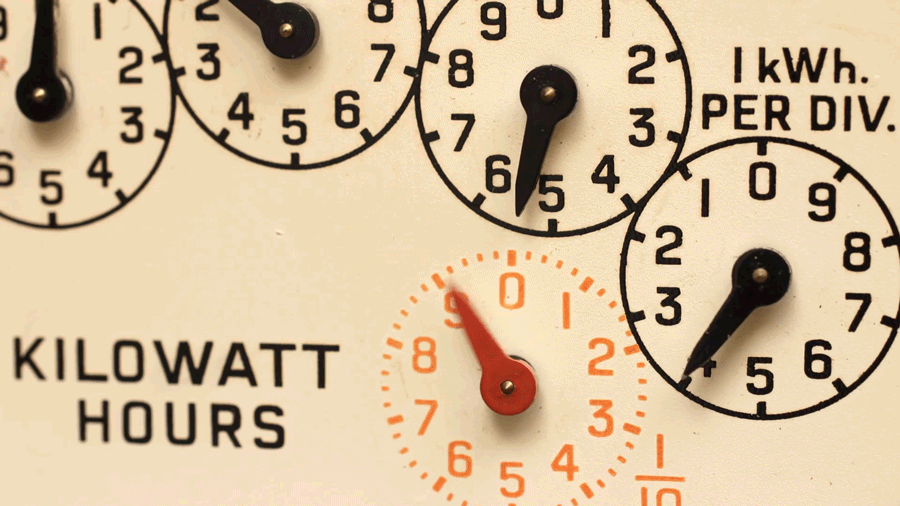
Every day we flick on lights, load dishwashers and boil kettles but few of us pause and think of the stress this can cause for the electricity system. We certainly don’t call National Grid in advance to let them know when we plan to do laundry.
But when any number of the 25.8 million households in Great Britain turn on a washing machine, the grid needs to be ready for it. Fortunately, these spikes in demand are often predictable.
“We are creatures of habit,” says Ian Foy, Drax Head of Ancillary Services.
“We all tend to come home from work at the same time and turn on similar appliances, and this keeps the shape of daily electricity demand much the same.”
National Grid, the operator of Great Britain’s high voltage power transmission system, uses this consistent demand to plan when and how much electricity will be needed for the coming days, and agrees contracts with generators to meet it.
However, there are times when the unexpected can happen – an unseasonable cold spell or a power station breakdown – causing sudden imbalances in supply and demand. To plan for this, the grid carries ‘reserve power’, which is used to fill these short-term gaps.
Delivering this doesn’t just mean keeping additional power stations running to deliver last minute electricity. Instead, it involves a range of services coming from different types of providers, technologies and timescales.
In Great Britain, there are four primary ways this is delivered.
-
Frequency response
The fastest form of reserve is frequency response. It is an automatic change in either electricity generation or demand in response to the system frequency deviating from the target 50Hz.
Generation and demand must be kept balanced within tight limits, second by second. Failure to do so could lead to the whole system becoming unstable, leading to the risk of blackouts. This is why, every second of the day, National Grid has power generators operating in Frequency Response mode. These power stations effectively connect their steam governor or fuel valves to a frequency signal. If frequency falls, generation increases. If frequency rises, generation is reduced.
An issue which has arisen over the past few years is a reduction in system inertia. The inertial forces in a spinning generator help slow the rate of frequency change, acting like dampers on car suspension. Some small power generation technologies, along with some demand, are sensitive to the rate of change of frequency – too high a rate can cause it to disconnect from the system and this unplanned activity can lead to system instability.
Some forms of generation such as wind and solar along with high voltage, direct current (HVDC) interconnectors between Great Britain and the rest of Europe do not provide inertia. As these electricity sources grow on the system, the system operator must find ways to accommodate them. Reducing the size of the largest credible loss, e.g. reducing interconnector load, buying faster frequency response or running conventional generation out of merit are the usual approaches.
-
Spinning reserve
The next quickest and most common reserve source, spinning reserve, can jump into action and start delivering electricity in just two minutes. This reserve, both positive and negative, is carried on multiple generating units often running at a part load position (for example, if Drax’s biomass Unit 3 is running at 350 MW of a possible 645 MW). Typical delivery rates are 10 to 20 MW per minute.
This type of reserve responds to unexpected short-term changes in power demand or changes in power generation either in size or timing. For example, during a major TV event or if a generator changes output unexpectedly.
During television ad breaks, the millions of people watching may switch on kettles or flick on lights, sending demand soaring. If a programme or sporting event does not end at the scheduled time, National Grid has to quickly change the generation schedule by sending an electronic dispatch to a generator who responds by quickly ramping up or down.
Thermal power stations such as Drax along with hydro and pumped storage, which can increase or decrease output on demand, are the most common providers of this form of reserve, but newer technologies such as batteries will also be able to offer the speed required.
-
Short term operating reserve (STOR)
A slightly slower cousin to spinning reserve, STOR is contracted months in advance by National Grid. It is designed to be available within 20 minutes’ notice.
Around 2 gigawatts (GW) of capacity can provide reserves against exceptionally large losses or demand spikes. STOR capacity tends to be plant which cannot make a living in the energy market because it has a high marginal cost. Traditionally STOR has been supplied by low efficiency aeroderivative turbines or diesel engines but a wider variety of technologies from batteries to demand reduction are increasingly being contracted.
-
Demand turn up
Managing reserve power isn’t just about finding extra generation to meet demand. Sometimes it’s about quickly addressing too much generation.
High levels of generation coming onto the grid without an equally high demand can overload power lines and networks, causing instability and frequency imbalances, which can lead to blackouts. This might happen in the summer months, when the weather allows for lots of intermittent renewable generation (such as wind and solar), but low levels of demand due to factors like warmer weather and longer daylight hours.
To restore balance, the grid is beginning to ask intensive commercial or industrial electricity users to increase consumption or turn off any of their own generation in favour of grid-provided power. In the case of generating units at Drax Power Station, the response starts less than a second from the initial frequency deviation to help slow the rate of frequency change and minimises large frequency swings.
Reserve in a changing energy system
Planning for the unexpected has long been a staple of the electricity system, but as the shape of that system changes, reserve and response delivery is having to change too.
“Carrying reserve is easier on conventional plants because you know what the plant is capable of generating,” says Foy.
“Wind and solar are subject to the weather, which changes over time. The certainty you get with conventional generation you don’t necessarily get with the intermittency of weather-dependant renewables.”
Add to that the way we use electricity, everything from high efficiency lighting, electric vehicles through to smart appliances and we can see the challenges will grow.
As more variable renewables hits the system, storage technologies will become more important in providing a fast-acting source of short term reserve and response. Smart appliance technology too will play a bigger role in spreading demand across the day and reducing the size of demand peaks and troughs which require rapid changes in generation.
Industry has a role to play too. Some of the biggest users of electricity are expected to play an increasingly important role in support of the system operator. National Grid told members of Parliament in 2016, that ‘it is our ambition to have 30-50% of our balancing capacity supplied by demand side measures by 2020.’
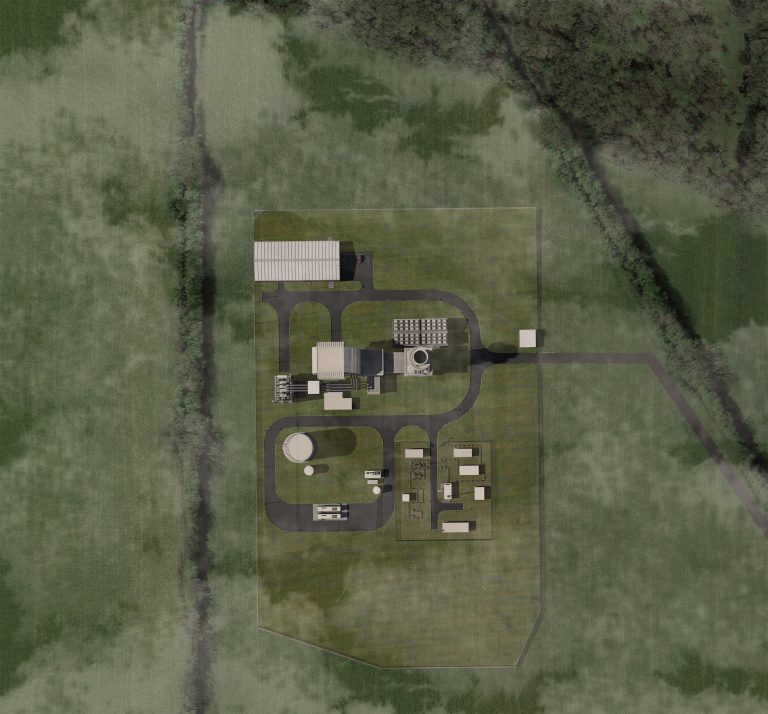
Artist’s impression of a Drax rapid-response gas power station (OCGT) with planning permission
Until these technologies and market mechanisms are widespread and implemented at scale across the grid, however, it will fall to thermal power stations such as biomass, gas turbines such as the planned Progress Power in Suffolk and, on occasion, coal to ensure there is the required reserve power available.
This short story is adapted from a series on the lesser-known electricity markets within the areas of balancing services, system support services and ancillary services. Read more about black start, system inertia, frequency response, and reactive power. View a summary at The great balancing act: what it takes to keep the power grid stable and find out what lies ahead by reading Balancing for the renewable future and Maintaining electricity grid stability during rapid decarbonisation.