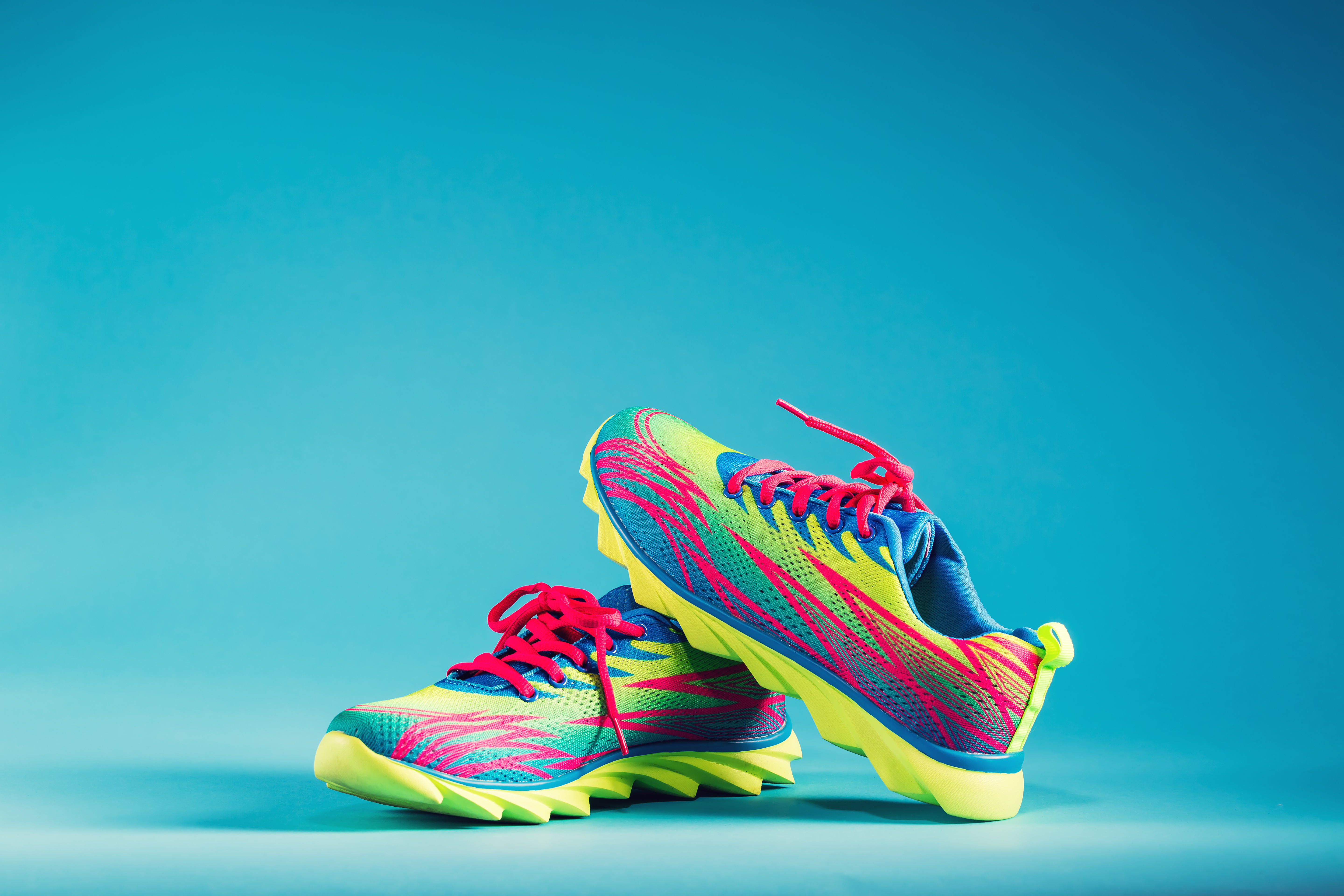
The combination of a heatwave and an entertaining world cup campaign put big demands on Great Britain’s beer supplies this summer. But European-wide carbon dioxide (CO2) shortages put a hold on that celebratory atmosphere as word spread that a lack of bubbles could result in the country running out of beer.
The drinks business managed to hold out, but the threat of long term CO2 shortages still lingers over the continent. One possible – and surprising – solution could lie in electricity generation, thanks to the capturing and storing of its carbon emissions.
Carbon capture and storage (CCS) is one of the key technologies in need of development to allow nations to meet their Paris Agreement goals. It has the potential to stop massive amounts of emissions entering the atmosphere, but it also raises the question: what happens to all that carbon once it’s captured?
Drax recently met with the British Beer & Pub Association to discuss using some of the carbon it plans to capture in its upcoming trial of Bioenergy Carbon Capture and Storage (BECCS) to keep the fizz in drinks.
It’s a novel solution to a potential problem, but it’s just one of the many emerging possibilities being developed around the world.
Smarter sneakers
Carbon capture is all about reducing carbon footprints – a phrase energy company NRG interpreted quite literally by creating ‘The Shoe Without A Footprint’. The white trainer was created to showcase the abilities of carbon capture, use and storage (CCuS) and is made of 75% material produced from captured emissions that have been turned into polymers, a molecular structure similar to plastics.
Only five pairs of the sneakers were created as part of NRG’s Carbon XPrize competition to find uses for captured carbon. However, they remain symbolic of the versatility offered by captured and stored carbon and its potential to contribute to the manufacture of everyday objects.
Better furniture
Finding an alternative to plastics is one of the key ways of facilitating a move away from global dependencies on crude oil. Sustainable materials company Newlight uses captured CO2 or methane emissions to create a bioplastic called AirCarbon – a thermopolymer, which means it can be melted down and reshaped.
The company has teamed up with IKEA, which will buy 50% of the 23,000 tonnes of bioplastic Newlight’s plant produces per year. It’s part of the Swedish furniture giant’s efforts to increase the amount of recycled materials it uses and means upcycled carbon could soon be appearing in millions of homes around the world.
Cleaner concrete
If the shoes people walk around on can be made from captured carbon, so too can the cities they walk within. Making concrete is a notoriously dirty process. Cement, the main binding agent in concrete, is thought to contribute to as much as 5% of the world’s greenhouse gas emissions, but this could change thanks to clever use and implementation of carbon capture technology.
At one level, CCS can be introduced to capture emissions from the manufacturing process. On another, the CO2 captured can be used as a raw material from which to create the concrete, effectively ‘locking in’ carbon and storing it for the long term.
Teams of engineers, material scientists and economists at UCLA who have worked on the problem for 30 years have succeeded in creating construction materials from CO2 emissions in lab conditions using 3D printing technology. Now it’s just a matter of scaling it up to industrial usage.
A metal alternative
Carbon nanotubes are stronger than steel but lighter than aluminium, which makes them a hugely useful material. They’re currently used in jets, sports cars and even in industrial structures, but producing them can be expensive and, until recently, could not utilise CO2 for manufacture. A team from George Washington University is changing that.
Its C2CNT technology splits captured CO2 into oxygen and carbon in a molten carbonate bath using electrolysis. From here the carbon is repurposed into carbon nanotubes at a high rate and lower cost than previous methods.
Future fuels
Transportation is one of the major emitters of carbon around the world, so any way it can be reduced or re-used in this field will be a huge positive. Carbon recycling company LanzaTech has developed a way to do this via a process that uses anaerobic bacteria to ferment emissions into cleaner chemicals and fuels.
Its first facility, opening this year in China, will create fuel-grade bioethanol that can be blended with gasoline to create vehicle fuel, or even converted into jet fuel with 65% lower greenhouse gas emissions.
Aviation, too, can benefit from carbon recycling through the creation of synthetic crude oil and gas using CO2. Technology company Sunfire is developing processes that combine hydrogen (set to become a major part of industry and transport) and biogenic CO2, (emissions from natural sources), to create synthetic hydrocarbons that could fuel planes.
From Silicon Valley to Valles Marineris
Earth isn’t the only place humans are innovating around carbon capture – at least, right now. With the race to send men and women to Mars stepping up, the challenges of dealing with its inhospitable atmosphere (which is 95% CO2) and ensuring a minimal human impact to the planet are becoming more acute. Carbon capture and use presents an opportunity to tackle both.
Californian company Opus 12 has developed a device that recycles CO2 from ambient air and industrial emissions and turns it into fuels and chemicals using only electricity and water. The device has the CO2 conversion power of 37,000 trees (or 64 football fields of dense forest) packed into the volume of a suitcase, and can convert CO2 into 16 different products.
In the long-term, the technology might provide critical services for human colonies on the Red Planet by capturing and using CO2 from the atmosphere or any future Mars-based factories. The Opus 12 device can also use ice (buried on the planet in places that could be accessible to astronauts) to convert Mars CO2 into plastic to make bricks and tools, methane that can form rocket fuel, and feedstocks for microbes to create medicine or food.
Turning pollution into possibilities
Many of these technologies are in their infancy, but the possibilities they present are very real. In fact, Drax’s upcoming trial of BECCS will see it capture and store as much as a tonne of carbon every day.
The proliferation of this technology in industry and electricity production – and the resultant increase in captured carbon – will help encourage more companies to see CO2 emissions as an opportunity for revenue while helping countries meet their Paris Agreement emissions goals.
Learn more about carbon capture, usage and storage in our series:
- Planting, sinking, extracting – some of the ways to absorb carbon from the atmosphere
- From capture methods to storage and use across three continents, these companies are showing promising results for CCUS
- Why experts think bioenergy with carbon capture and storage will be an essential part of the energy system
- The science of safely and permanently putting carbon in the ground
- The numbers must add up to enable negative emissions in a zero carbon future, says Drax Group CEO Will Gardiner.
- The power industry is leading the charge in carbon capture and storage but where else could the technology make a difference to global emissions?
- From NASA to carbon capture, chemical reactions could have a big future in electricity
- A roadmap for the world’s first zero carbon industrial cluster: protecting and creating jobs, fighting climate change, competing on the world stage
- Can we tackle two global challenges with one solution: turning captured carbon into fish food?
- How algae, paper and cement could all have a role in a future of negative emissions
- How the UK can achieve net zero
- Drax CEO addresses Powering Past Coal Alliance event in Madrid, unveiling our ambition to play a major role in fighting the climate crisis by becoming the world’s first carbon negative company