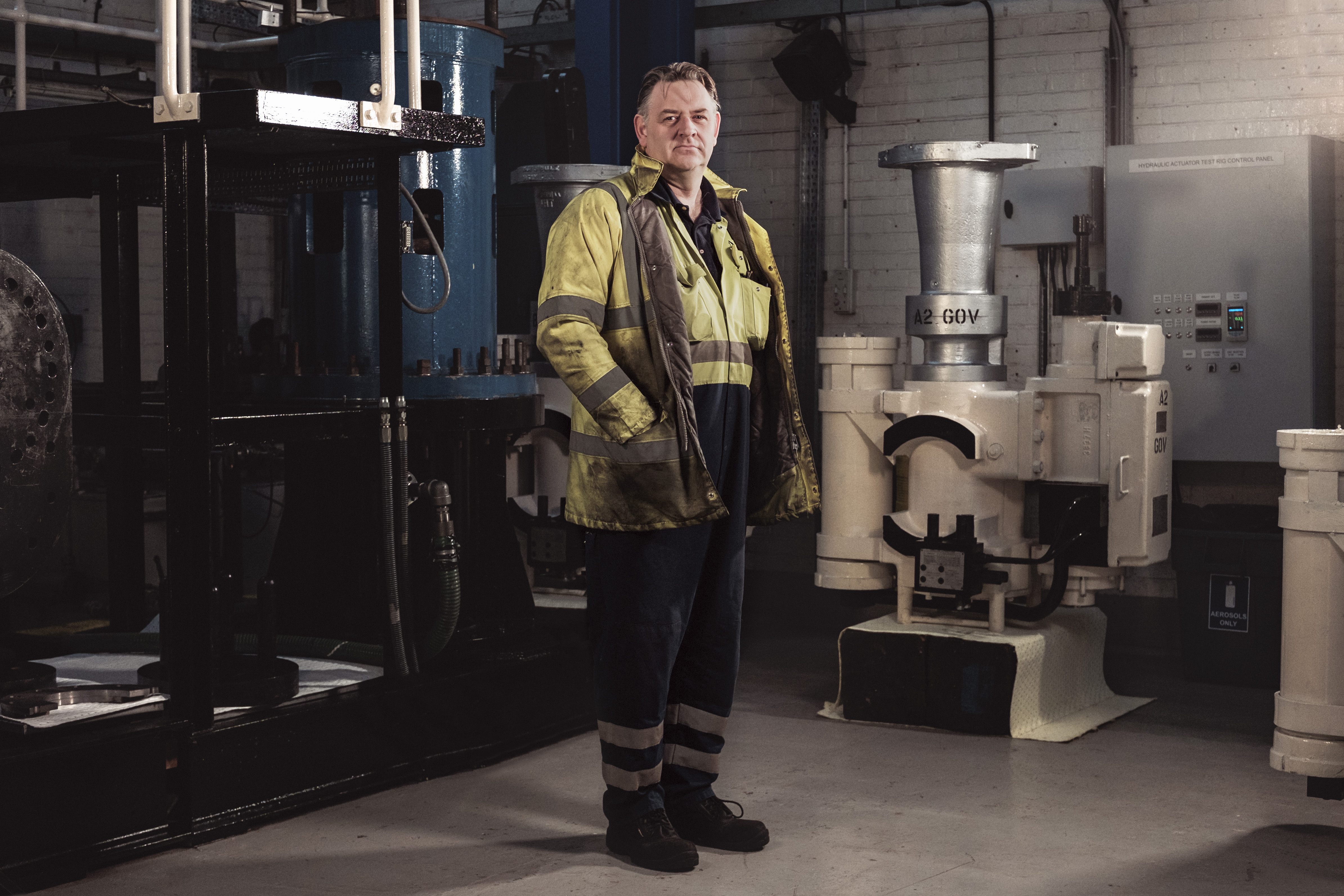
Before Drax Power Station was a part of Andrew Storr’s career, it was a part of his local environment.
“When I was at school in Selby they were building the second half of the station,” he says. “We could see them building the cooling towers out of the classroom windows.”
But it wasn’t until a careers advisor brought an old cine film of the power station into class that he considered working there. “Part of the film was them stripping the turbine and I watched it and thought, ‘I want to do that,’” he says.
Today, Storr does more than strip the turbines, he’s part of the engineering team that oversees them – a job that needs to be taken seriously.
“If the turbine’s off, forget the rest of it: we’re not generating electricity ,” he says. “We’ve got to make sure the turbine and the generator are absolutely as bulletproof as possible because we’ve only got one per unit.”
Considering the conditions each one comes under, this is no easy task. “The turbine shaft weighs 300 tonnes and spins at 3,000 rpm. The high pressure turbine is 165 bar, and temperature-wise, the steam running through it making it spin is 565 degrees centigrade.”
Bulletproof is an understatement. When it comes to carrying out maintenance on a turbine, it’s more than likely you’ll have to visit Storr’s workshop.
Fixing the governor
The workshop hasn’t always been there. It all started fifteen years ago when a piece of equipment broke. It was a turbine governor relay, a precision hydraulic actuator that keeps the turbine spinning at the right speed. Drax needed a new one.
“They’ve got to be 100% reliable,” Storr explains. “If they lose control of the turbine, it can either come to a grinding halt or speed up too much and self-destruct.”
The team went in search of a replacement, contacting a manufacturer who came back with a sky-high quote. But Storr’s boss at the time had another idea.
He asked whether Storr could reverse engineer a full set of governor relays. “I made the fatal mistake of saying, ‘Yeah!’ So I set off with a few photographs and a handful of sketches,” Storr explains.
What followed were sleepless nights and a lot of grey hair, but in the end he managed to reproduce a full set that cost nearly half of the original quote. Better than that, they worked perfectly.
“Today, they’re on Unit 5, doing the business.”
Building the workshop
Manufacturing the governor relays was a turning point. Storr and the team saw there could be further savings and benefits if they did more manufacturing or refurbishment in-house. They had the staff capable of doing it, they just needed the facilities.
Although there was some initial scepticism from some in the company, Drax armed Storr with a small budget and he set out on building the workshop. That was 15 years ago. Back then, the workshop was designed to only refurbish equipment, but it has since grown. Now they can manufacture, too.
Today, when Drax buys in equipment which is either very expensive or lacking in quality, Storr’s team can modify it, make it fit better, last longer, or improve its efficiency without sending it away from the plant and incurring extra costs.
“We’re reaping the rewards. We’re leagues in front of everyone else in the UK because we’ve got our own manufacturing and machining facility,” Storr says. “We can do all this work on site. We’re not relying on other people.”
The workshop has given Drax an edge when it comes to its engineering ability, but Storr remains modest about the achievement.
“The thing is,” he says, “I’ve got a good boss and he will support you. But I do see it as a bit of a feather in my cap.”