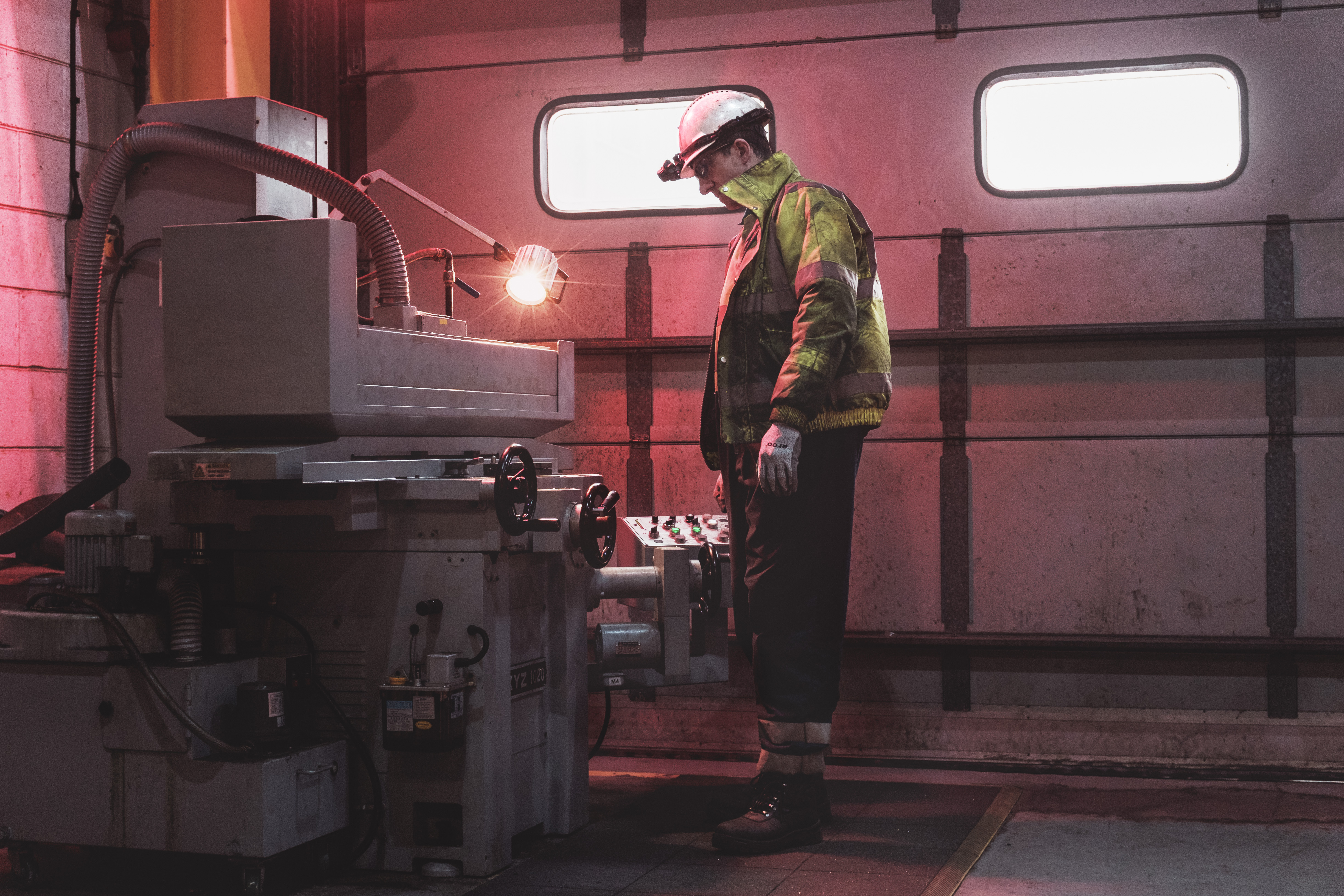
A klaxon sounds and a crane big enough to lift 160 tonnes moves slowly across the inside of a cavernous warehouse. Below, a team of engineers stand around a turbine spindle the size of a double decker bus but weighing four times as much at 65 tonnes, waiting for the crane’s descent.
Around them, other engineers work on similar-sized equipment. One uses a wrench the size of an arm. Another programs a computerised lever to carefully strip millimetres from a piece of steel. It’s just a normal day inside Drax Power Station’s machine workshop.
For the last 15 years, this workshop has been refurbishing, repairing and manufacturing tools and equipment for use at the power station – a fact that sets Drax apart from other stations like it.
“We’re envied by a few stations because we do most things in-house,” says Turbine Engineer and head of the workshop, Andrew Storr. “We’re leagues in front of everyone else in the UK because we’ve got our own manufacturing and machining facility. We can do all this work on site. We’re not relying on other people.”
Storr set up the workshop in 2001 after being asked to reverse engineer a replacement set of governor relays (components that help regulate the flow of steam going into the turbines) for one of Drax’s steam turbines. Today, it’s a thriving centre of activity filled with heavy-duty machinery and ingenious engineers.
A look inside the workshop
“When you’re manufacturing spares it’s not a matter of going down to our machine shop and just saying ‘make one of those’. You’ve got to have the correct grade of material, the correct size, the correct certification for the material – you can’t just have a scrappy piece of steel that you find. It’s got to have paperwork with it to say it’s certified up to whatever it’s supposed to be,” says Storr.
Turbine bearings need to be bored to size using a horizontal borer that very accurately shaves out the lining of the inner bearing. Getting it right is incredibly important, explains Storr: “If it’s made too large it causes the turbine shaft to vibrate. If it’s made too small the bearing becomes too hot and the white metal will melt and pour out the bearing. We need to avoid both of these issues at all cost.”
The inside of the turbine blading needs to have seal strips administered by hand as they’re delicately made to limit any damage to the spinning shaft should they touch each other. Despite the wealth of equipment at the disposal of the team in the shop, success depends on the skill of the engineers using it.
There are three 160-tonne cranes in the turbine hall, each installed before the turbines were built. This meant the construction companies who erected the turbines could lift all heavy components into place with ease. “Due to their size they move slowly. It takes approximately 20 minutes for the largest hook to travel from the ground all the way to the top,” says Storr.
“In mechanical engineering it’s sometimes necessary to fit one part inside another, and once these parts are assembled they must stay locked together and not come apart,” Storr says. One way the team does this is by shrinking some components, and for this they use liquid nitrogen.
The team places the component that needs to fit inside another into a bath of liquid nitrogen and shrink it at -190 degrees Celsius. Once shrunk, the team assembles the two, placing the now smaller component into the larger one. “Eventually the inner part warms up to ambient temperature and grows in size, making the fit very tight and preventing them from coming apart,” explains Storr.
In the past, Drax would send the work they now do in the machine shop to companies off site. And because all other power stations in the area would do the same thing, wait times would often be long and the quality of the output could vary.
“When we do it in-house I can keep my eye on it,” says Storr. “I can re-prioritise things depending on what is going to be needed back on the turbine first – we’ve got 100% control over it. We can make sure everything’s hunky-dory.”