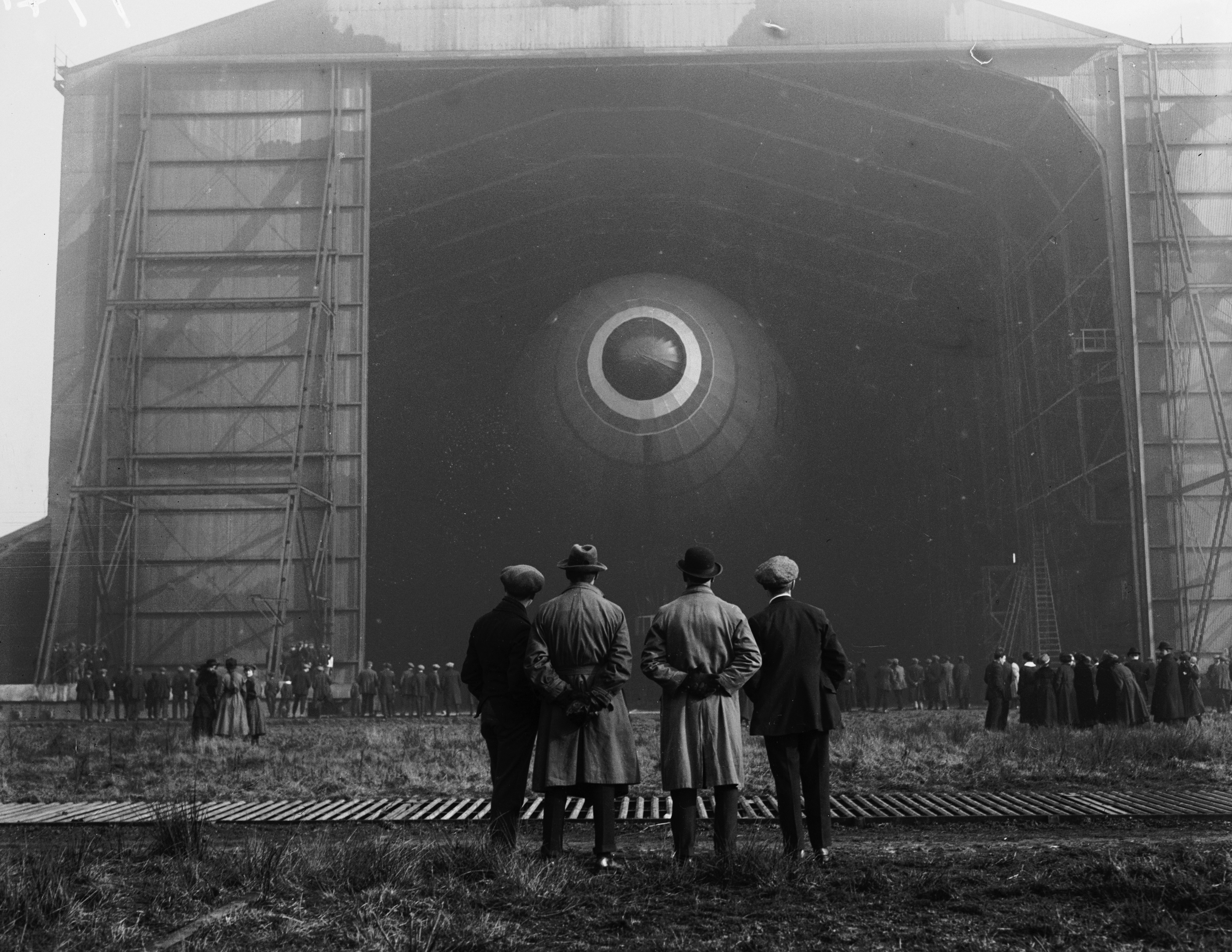
Barlow Mound is a haven for wildlife. More than 100 different species call it home, including kingfishers, roe deer and falcons. It’s an area that looks like it’s never been touched by the industrialisation that surrounds it. The truth is very different.
Barlow mound is manmade. It was built in the 1970s using residue material from its neighbour Drax Power Station. It’s a success story of using what was then considered a waste material to create something natural and beautiful. But it has a long history before becoming what it is today and to explore that history is to track the outlook of the UK over the last millennium.
The military moves in
The area around Barlow and Drax was an important location for the very first Viking explorers who arrived here from the North Sea via the region’s Ouse and Aire rivers. But it wasn’t until 1086 that it received its first recorded mention, when it was listed as ‘Berlai-leag’ in the Domesday Book.
Translating to ‘a clearing where barley grew’, it was named by Anglo Saxon settlers, who established the region as a mix of farmland, fields and woodlands and it remained agricultural until the early twentieth century, when the country was plunged into war.
When the First World War began in 1914 and the need for new war machines arose, Sir W G Armstrong Whitworth & Co Ltd, a manufacturing company which had obtained the land in 1913 from the estate of Lord Londesborough, set up an airship factory on the site.
During its lifetime the factory constructed three airships, the 25r, R29 and R33, but when WWI ended and demand for airships sank, the factory shut down and the land passed to the Ministry of Defence (MOD).
During the Second World War the area became an important location in the country’s war efforts once again. The MOD set up an army ordnance and command supply depot manufacturing and storing items like mess tins and kerosene lamps. At one point the site also included a Prisoner of War camp.
By the 60s the UK’s needs for defence manufacturing had subsided. Instead, what it needed was more power. With the rich coal seams of the area and the existing rail network (the Hull-Barnsley line ran through), building a power station in the Barlow area was an obvious solution.
First-of-a-kind solution
In 1967 the land was bought by the Central Electric Generating Board (CEGB) which began the construction of Drax Power Station. One of the early challenges it faced was how to minimise the environmental impact to the surrounding countryside.
In particular, it needed a solution for the tonnes of ash that came from the burning of coal fuel, which included both pulverised fuel ash (PFA) and furnace bottom ash (FBA). The answer was a first-of-a-kind: build a mound using the materials.
Construction on Barlow Mound began in 1974. First the existing top soil was removed and preserved for later use, drains were added and then a layer of FBA was laid.
Next conditioned PFA was added and moulded to suit the original design, never reaching higher than 36 metres. At this height the mound would visually obscure the power station from the neighbouring houses.
The final step was to seal the mound with a polymer and then reintroduce the top soil before grass, trees and hedgerow were planted. The trees and plants had been carefully tested to ensure that their roots wouldn’t interfere with the ash and compromise the integrity of the structure.
An ecologically important area
As time has passed and Drax Power Station has produced more ash, the mound has developed and grown. More than 301 million m3 is stored in the current site – more than the capacity of three million double decker buses.
In addition to the 100 species living on the site, a tenant farmer works 20 fields and a swan rescue and wildlife hospital rehabilitates up to 2,000 birds a year. More recently, the Skylark Centre and Nature Reserve has now opened up the area to the public to explore walking trails and see the nature first-hand.
Barlow is an area that has changed consistently since 1086. From the North’s early beginnings as an agricultural hub and Anglo-Saxon settlement, to the necessity for large-scale power solutions and to the importance of preserving local ecology, Barlow is an area that has been characterised by the outlook of the country.
Like Drax Power Station, to which it is intrinsically linked, Barlow Mound is a part of the Northern Yorkshire landscape – literally and figuratively.