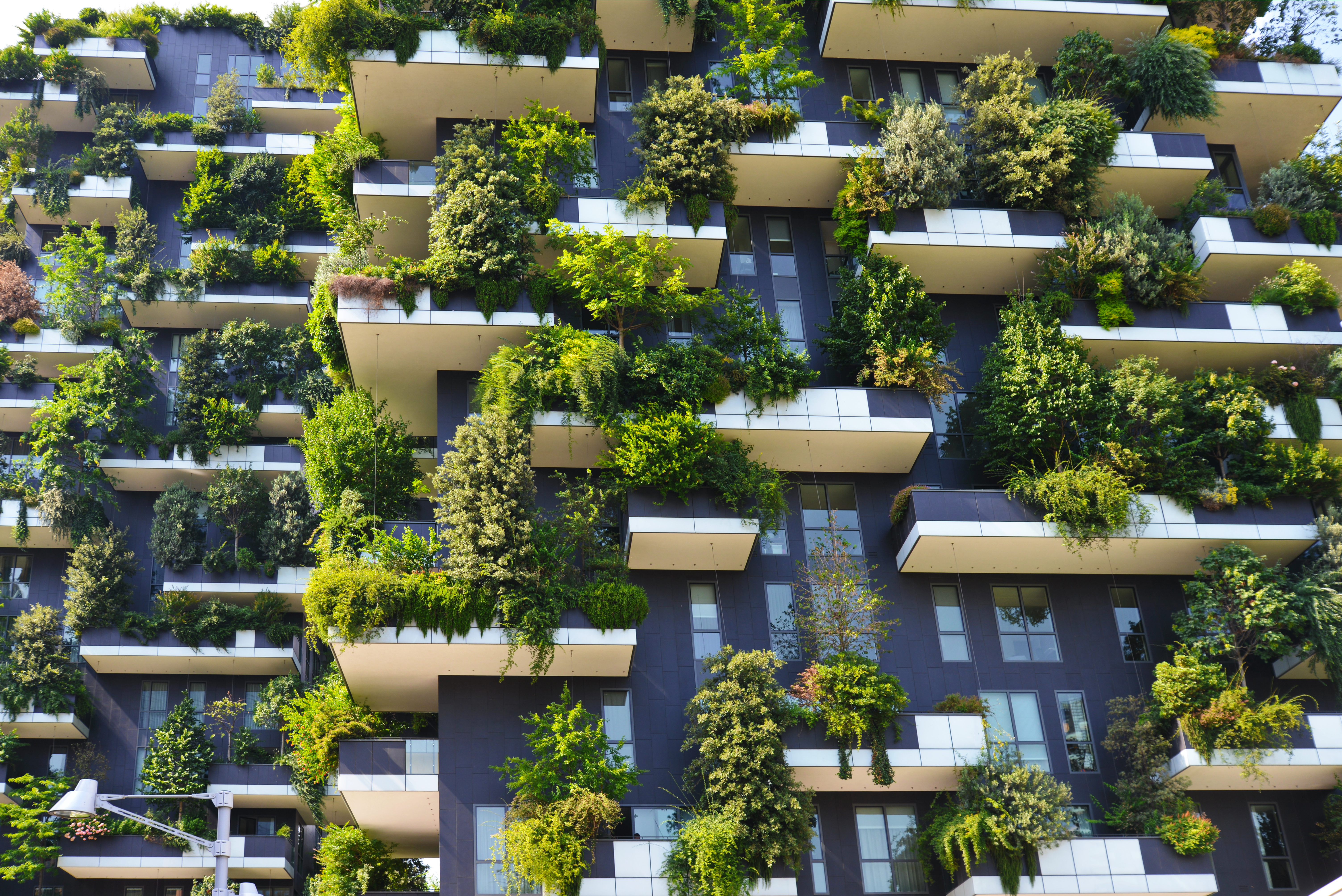
For age-old rivals Glasgow and Edinburgh, the race to the top has taken a sharp turn downwards. Instead, they’re in a race to the bottom to earn the title of the first ‘net zero’ carbon city in the UK.
While they might be battling to be the first in the UK to reach net zero, they are far from the only cities with net zero in their sights. In the wake of the growing climate emergency, cities, companies and countries around the world have all announced their own ambitions for hitting ‘net zero’.
It has become a global focus based on necessity – for the world to hit the Paris Agreement targets and limit global temperature rise to under two degrees Celsius, it’s predicted the world must become net zero by 2070.
Yet despite its ubiquity, net zero is a term that’s not always fully understood. So, what does net zero actually mean?
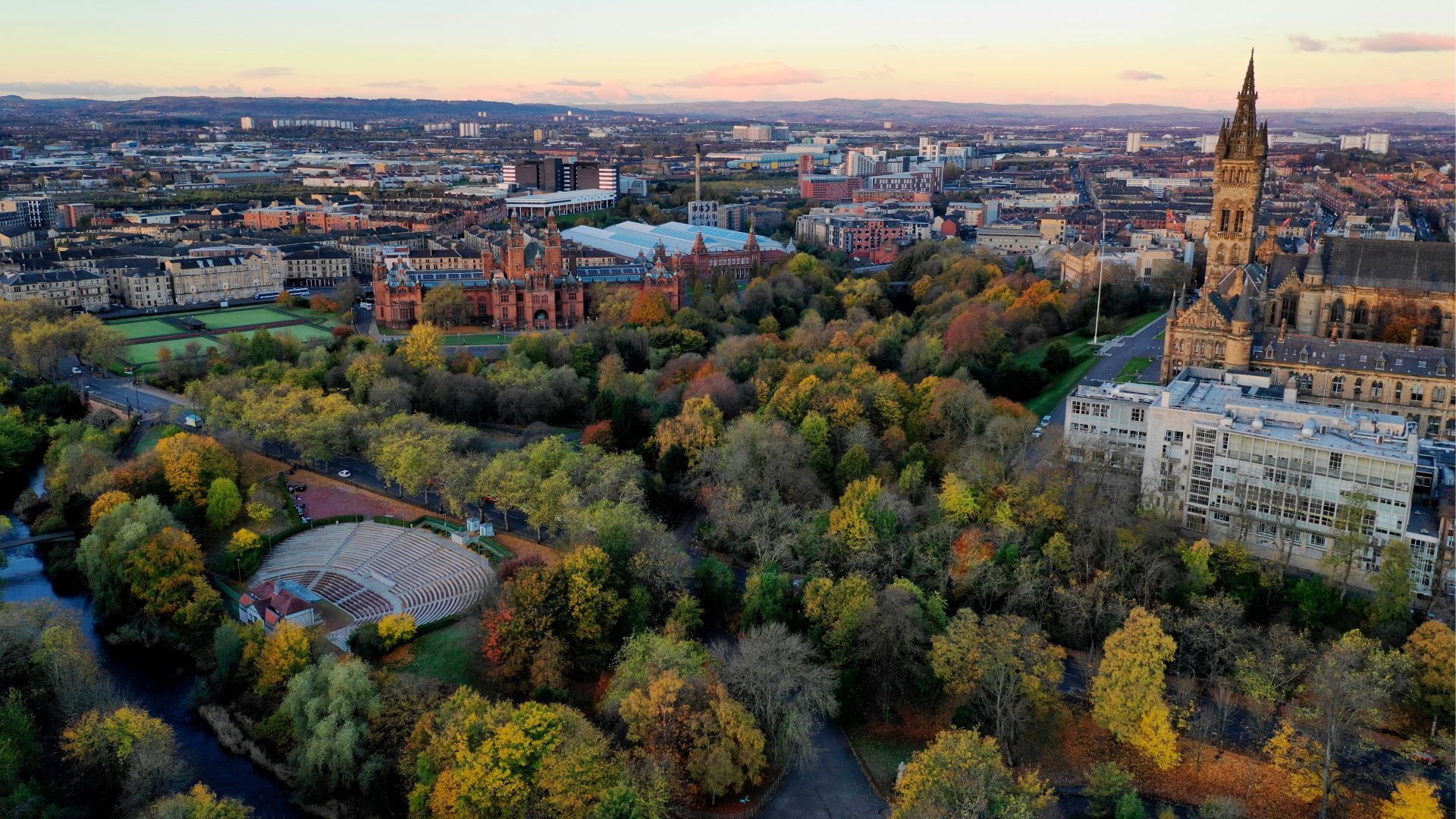
Glasgow, Scotland. Host of COP26.
What does net zero mean?
‘Going net zero’ most often refers specifically to reaching net zero carbon emissions. But this doesn’t just mean cutting all emissions down to zero.
Instead, net zero describes a state where the greenhouse gas (GHG) emitted [*] and removed by a company, geographic area or facility is in balance.
In practice, this means that as well as making efforts to reduce its emissions, an entity must capture, absorb or offset an equal amount of carbon from the atmosphere to the amount it releases. The result is that the carbon it emits is the same as the amount it removes, so it does not increase carbon levels in the atmosphere. Its carbon contributions are effectively zero – or more specifically, net zero.
The Grantham Research Institute on Climate Change and the Environment likens the net zero target to running a bath – an ideal level of water can be achieved by either turning down the taps (the mechanism adding emissions) or draining some of the water from the bathtub (the thing removing of emissions from the atmosphere). If these two things are equally matched, the water level in the bath doesn’t change.
To reach net zero and drive a sustained effort to combat climate change, a similar overall balance between emissions produced and emissions removed from the atmosphere must be achieved.
But while the analogy of a bath might make it sound simple, actually reaching net zero at the scale necessary will take significant work across industries, countries and governments.
How to achieve net zero
The UK’s Committee on Climate Change (CCC) recommends that to reach net zero all industries must be widely decarbonised, heavy good vehicles must switch to low-carbon fuel sources, and a fifth of agricultural land must change to alternative uses that bolster emission reductions, such as biomass production.
However, given the nature of many of these industries (and others considered ‘hard-to-treat’, such as aviation and manufacturing), completely eliminating emissions is often difficult or even impossible. Instead, residual emissions must be counterbalanced by natural or engineered solutions.
Natural solutions can include afforestation (planting new forests) and reforestation (replanting trees in areas that were previous forestland), which use trees’ natural ability to absorb carbon from the atmosphere to offset emissions.
On the other hand, engineering solutions such as carbon capture usage and storage (CCUS) can capture and permanently store carbon from industry before it’s released into the atmosphere. It is estimated this technology can capture in excess of 90% of the carbon released by fossil fuels during power generation or industrial processes such as cement production.
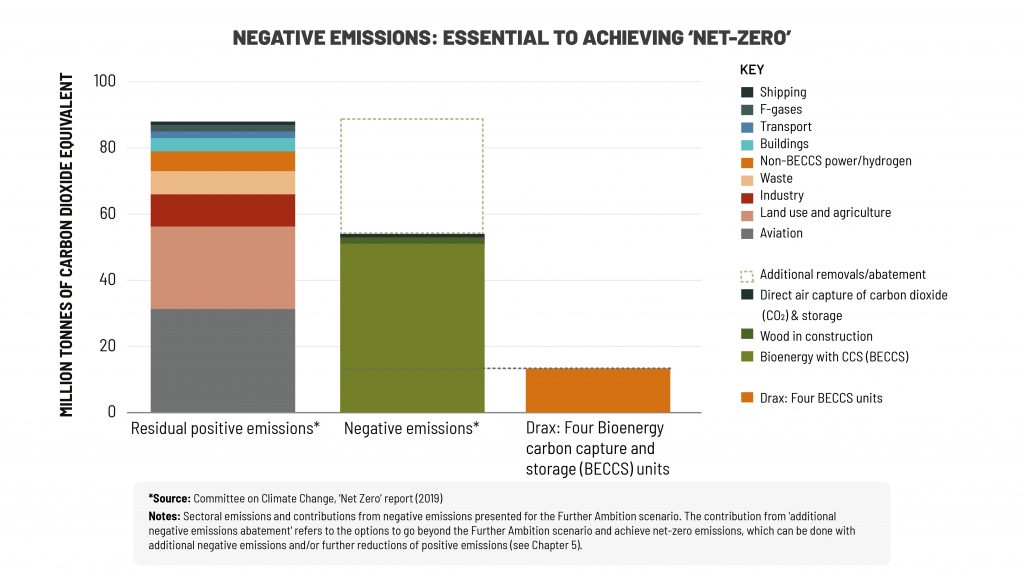
Click to view/download graphic. Source: Zero Carbon Humber.
Bioenergy with carbon capture and storage (BECCS) could actually take this a step further and lead to a net removal of carbon emissions from the atmosphere, often referred to as negative emissions. BECCS combines the use of biomass as a fuel source with CCUS. When that biomass comes from trees grown in responsibly managed working forests that absorb carbon, it becomes a low carbon fuel. When this process is combined with CCUS and the carbon emissions are captured at point of the biomass’ use, the overall process removes more carbon than is released, creating ‘negative emissions’.
According to the Global CCS Institute, BECCS is quickly emerging as the best solution to decarbonise emission-heavy industries. A joint report by The Royal Academy of Engineering and Royal Society estimates that BECCS could help the UK to capture 50 million tonnes of carbon per year by 2050 – eliminating almost half of the emissions projected to remain in the economy.
The UK’s move to net zero
In June 2019, the UK became the first major global economy to pass a law to reduce all greenhouse gas emissions to net zero by 2050. It is one of a small group of countries, including France and Sweden, that have enacted this ambition into law, forcing the government to take action towards meeting net zero.
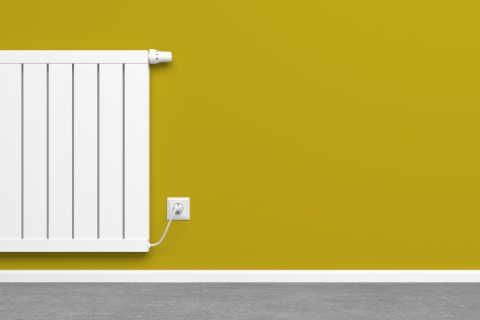
Electrical radiator
Although this is an ambitious target, the UK is making steady progress towards it. In 2018 the UK’s emissions were 44% below 1990 levels, while some of the most intensive industries are fast decarbonising – June 2019 saw the carbon content of electricity hit an all-time low, falling below 100 g/kWh for the first time. This is especially important as the shift to net zero will create a much greater demand for electricity as fossil fuel use in transport and home heating must be switched with power from the grid.
Hitting net zero will take more than just this consistent reduction in emissions, however. An increase in capture and removal technologies will also be required. On the whole, the CCC predict an estimated 75 to 175 million tonnes of carbon and equivalent emissions will need to be removed by CCUS solutions annually in 2050 to fully meet the UK’s net zero target.
This will need substantial financial backing. The CCC forecasts that, at present, a net zero target can be reached at an annual resource cost of up to 1-2% of GDP between now and 2050. However, there is still much debate about the role the global carbon markets need to play to facilitate a more cost-effective and efficient way for countries to work together through market mechanisms.
Industries across the UK are starting to take affirmative action to work towards the net zero target. In the energy sector, projects such as Drax Power Station’s carbon capture pilots are turning BECCS increasingly into a reality ready to be deployed at scale.
Along with these individual projects, reaching net zero also requires greater cooperation across the industrial sectors. The Zero Carbon Humber partnership between energy companies, industrial emitters and local organisations, for example, aims to deliver the UK’s first zero carbon industrial cluster in the Humber region by the mid-2020s.
Nonetheless, efforts from all sectors must be made to ensure that the UK stays on course to meet all its immediate and long-term emissions targets. And regardless of whether or not Edinburgh or Glasgow realise their net zero goals first, the competition demonstrates how important the idea of net zero has become and society’s drive for real change across the UK.
Drax has announced an ambition to become carbon negative by 2030 – removing more carbon from the atmosphere than produced in our operations, creating a negative carbon footprint. Track our progress at Towards Carbon Negative.
[*] In this article we’ve simplified our explanation of net zero. Carbon dioxide (CO2) is the most abundant greenhouse gas (GHG). It is also a long-lived GHG that creates warming that persists in the long term. Although the land and ocean absorb it, a significant proportion stays in the atmosphere for centuries or even millennia causing climate change. It is, therefore, the most important GHG to abate. Other long-lived GHGs include include nitrous oxide (N2O, lifetime of circa 120 years) and some F-Gasses (e.g. SF6 with a lifetime of circa 3,200 years). GHGs are often aggregated as carbon dioxide equivalent (abbreviated as CO2e or CO2eq) and it is this that net zero targets measure. In this article, ‘carbon’ is used for simplicity and as a proxy for ‘carbon dioxide’, ‘CO2‘, ‘GHGs’ or ‘CO2e’.