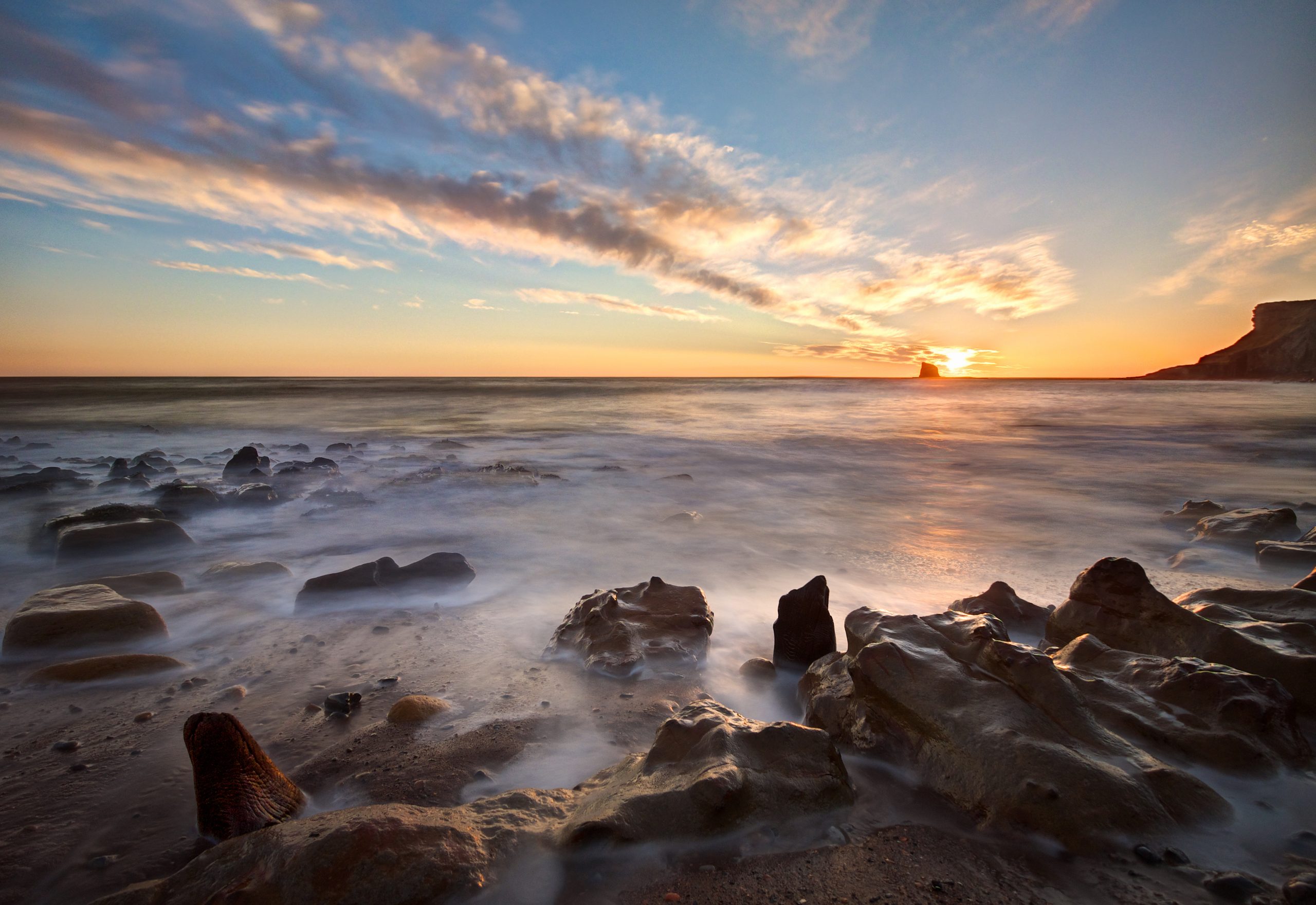
The North Sea has long shaped British trade. It’s also been instrumental in how the country is powered, historically providing an abundant source of oil and natural gas. However, this cold fringe off the North Atlantic could also play a vital role in decarbonising the UK’s economy – not because of its full oil and gas reservoirs, but thanks to its empty ones.
In an effort to limit or reduce the amount of carbon dioxide (CO2) in the atmosphere, countries around the world are rushing towards large scale carbon capture usage and storage projects (CCUS). In this process, CO2 is captured from sources, such as energy production and manufacturing, or directly removed from the air, and reused or stored permanently – for example, underground in disused oil and gas reservoirs or other suitable geological formations.
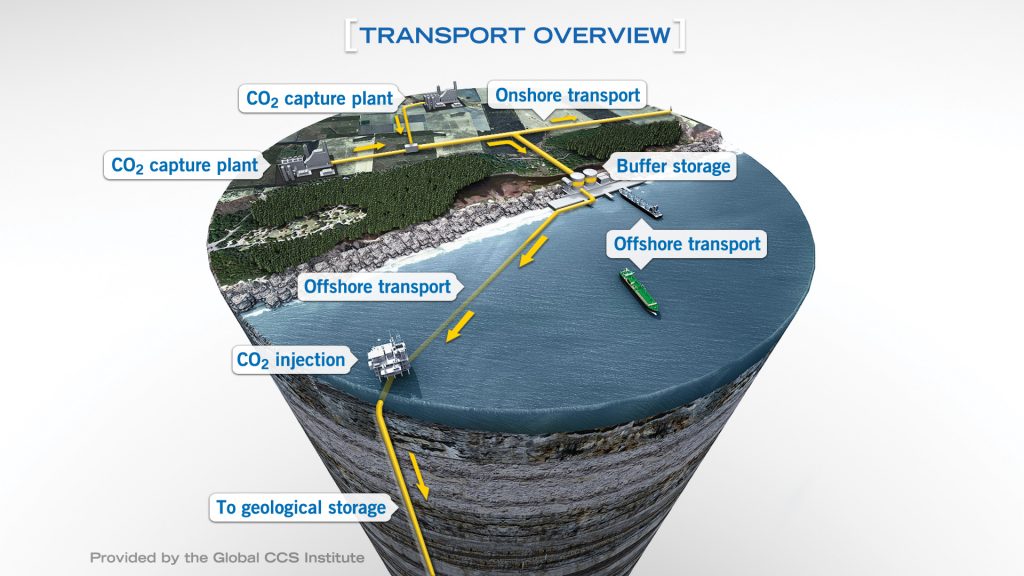
Source: CCS Image Library, Global CCS Institute [Click to view/download]
It’s clear the global capacity for CCUS must accelerate rapidly in the coming decade, but it raises the questions: where can these millions of tonnes of CO2 be stored, and what happens to it once it is?
Where can you store CO2?
The most well-developed approach to storing CO2 is injecting it underground into naturally occurring, porous rock formations such as former natural gas or oil reservoirs, coal beds that can’t be mined, or saline aquifers. These are deep geological formations with deposits of very salty water present in the rock’s pores and most commonly found under the ocean. The North Sea and the area off the US Gulf Coast contain several saline aquifers.
Once CO2 has been captured using CCUS technology, it’s pressurised and turned into a liquid-like form known as ‘supercritical CO2’. From there it’s transported via pipeline and injected into the rocks found in the formations deep below the earth’s surface. This is a process called geological sequestration.
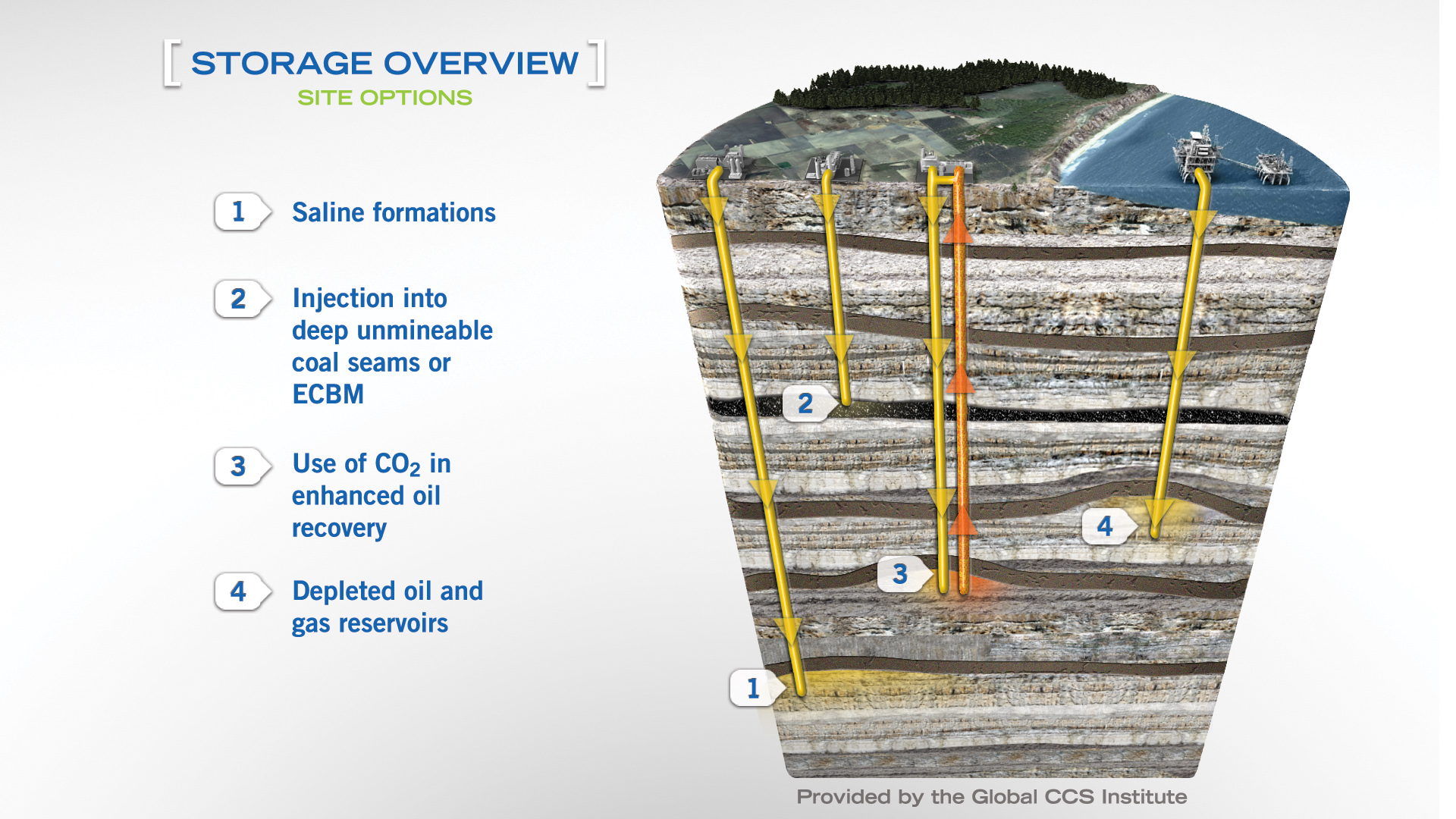
Source: CCS Image Library, Global CCS Institute [Click to view/download]
Keeping the lid on CO2 stored underground
Put simply, the most straightforward way underground reservoirs store CO2 is through the solid impermeable rock that typically surrounds them. Once CO2 is injected into a reservoir, it slowly moves upwards through the reservoir until it meets this layer of impermeable rock, which acts like a lid the CO2 cannot pass through. This is what’s referred to as ‘structural storage’ and is the same mechanism that has kept oil and gas locked underground for millions of years.

White chalk stone
Over time, the CO2 trapped in reservoirs will often begin to chemically react with the minerals of the surrounding rock. The elements bind to create solid, chalky minerals, essentially locking the CO2 into the rock in a process called ‘mineral storage’.
In the case of saline aquifers, as well as structural and mineral storage, the CO2 can dissolve into the salty water in a process called ‘dissolution storage’. Here, the dissolved CO2 slowly descends to the bottom of the aquifer.
In any given reservoir, each (or all) of these processes work to store CO2 indefinitely. And while there remains some possibility of CO2 leakage from a site, research suggests it will be minimal. One study, published in the journal Nature, suggests more than 98% of injected CO2 will remain stored for over 10,000 years.
Storage for the net zero future
In the United States, industrial scale storage is in action in Texas, Wyoming, Oklahoma and Illinois, and there are projects in progress across the United Arab Emirates, Australia, Algeria and Canada. However, there is still a long way to go for CCUS to reach the scale it needed to limit the effects of climate change.
Research has shown that globally, there is an abundance of CO2 storage sites, which could support widespread CCUS adoption. A report compiled by researchers at Imperial College London and E4tech and published by Drax details an estimated 70 billion tonnes of storage capacity in the UK alone. The US, on the other hand, has an estimated storage capacity of 10 trillion tonnes.
It’s clear the capacity for storage is present, it now remains the task of governments and companies to ramp up CCUS projects to begin to reach the scale necessary.
In the UK, Drax Power Station is piloting bioenergy carbon capture and storage projects (BECCS), which could see it becoming the world’s first negative emissions power station. As part of the Zero Carbon Humber partnership, it could also form a part of the world’s first zero carbon industrial hub in the north of the UK.
Such projects are indicative of the big ambitions CCUS technology could realise – not just decarbonising single sites, but capturing and storing CO2 from entire industries and regions. There is still a way to go to meet that ambition, but it is clear the resources and knowledge necessary to get there are ready to be utilised.

Source: Zero Carbon Humber [Click to view/download]
Learn more about carbon capture, usage and storage in our series:
- Planting, sinking, extracting – some of the ways to absorb carbon from the atmosphere
- From capture methods to storage and use across three continents, these companies are showing promising results for CCUS
- Why experts think bioenergy with carbon capture and storage will be an essential part of the energy system
- The numbers must add up to enable negative emissions in a zero carbon future, says Drax Group CEO Will Gardiner.
- The power industry is leading the charge in carbon capture and storage but where else could the technology make a difference to global emissions?
- From NASA to carbon capture, chemical reactions could have a big future in electricity
- A roadmap for the world’s first zero carbon industrial cluster: protecting and creating jobs, fighting climate change, competing on the world stage
- Can we tackle two global challenges with one solution: turning captured carbon into fish food?
- How algae, paper and cement could all have a role in a future of negative emissions
- How the UK can achieve net zero
- Transforming emissions from pollutants to products
- Drax CEO addresses Powering Past Coal Alliance event in Madrid, unveiling our ambition to play a major role in fighting the climate crisis by becoming the world’s first carbon negative company